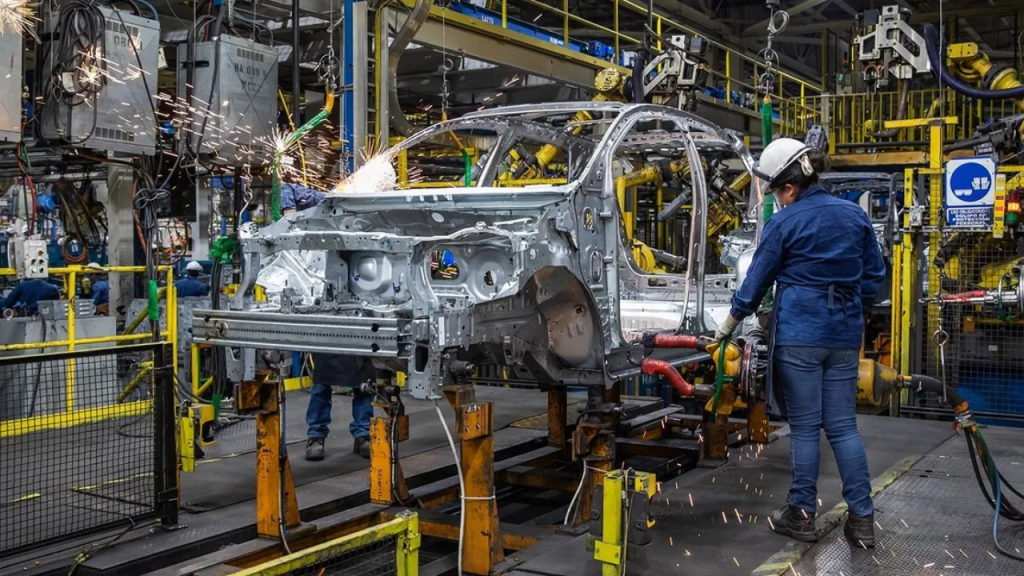
When President Donald Trump recently hinted at a possible reprieve from the 25% auto tariffs, his message was clear: automakers need more time to shift or increase vehicle production in the U.S. to meet his demand.
“They need a little bit of time because they’re going to make them here,” Trump stated on April 14. However, while this suggestion may sound simple, the reality of increasing U.S. car manufacturing is much more complicated.
Tariffs and Costs: The First Challenge
Trump’s plan to extend the timeline for automakers to increase U.S. production sounds promising, but it overlooks one key obstacle: tariffs. A 25% tariff on auto parts is set to go into effect by May 3, 2025.
This could raise the overall cost of vehicles even if they are assembled in the U.S., putting an added financial burden on manufacturers and consumers alike.
Beyond the tariffs, relocating or setting up new production plants in the U.S. is not a simple process. It takes years of planning, construction, and investment. This means that even with Trump’s extended timeline, automakers face a significant challenge in meeting his demands.
Relocating Production: A Long and Costly Process
The idea of moving car production to the U.S. is not as simple as politicians or some industry advocates make it seem. A new production facility requires extensive planning and investment. Automakers must consider factors such as land acquisition, infrastructure development (including energy and water supplies), labor hiring, and establishing supply chains for parts.
Building a new assembly plant can take years, with permitting alone taking anywhere from six months to over a year. After that, constructing the plant itself can take an additional 12 to 18 months, or even longer.
After the plant is built, automakers still need time for tooling, testing, and ramping up production to full capacity. This process can take anywhere from a year to several years, depending on the scale of the plant.
Large-Scale Plants: A Complex Endeavor
For Trump’s vision of increased U.S. production to come to life, large, multibillion-dollar assembly plants need to be built. These plants employ thousands of workers and require extensive infrastructure to operate.
Automakers like Hyundai have already committed to building such plants in the U.S. However, this is not a quick fix.
Hyundai’s new $12.6 billion “Metaplant” in Georgia, touted as a success for American manufacturing, took approximately two and a half years to complete.
The plant, which can produce up to 300,000 vehicles annually, will also employ about 8,500 people by 2031. Even with the massive investment and resources, the project is far from a fast process.
The Reality of Speed: Can U.S. Production Be Increased Quickly?
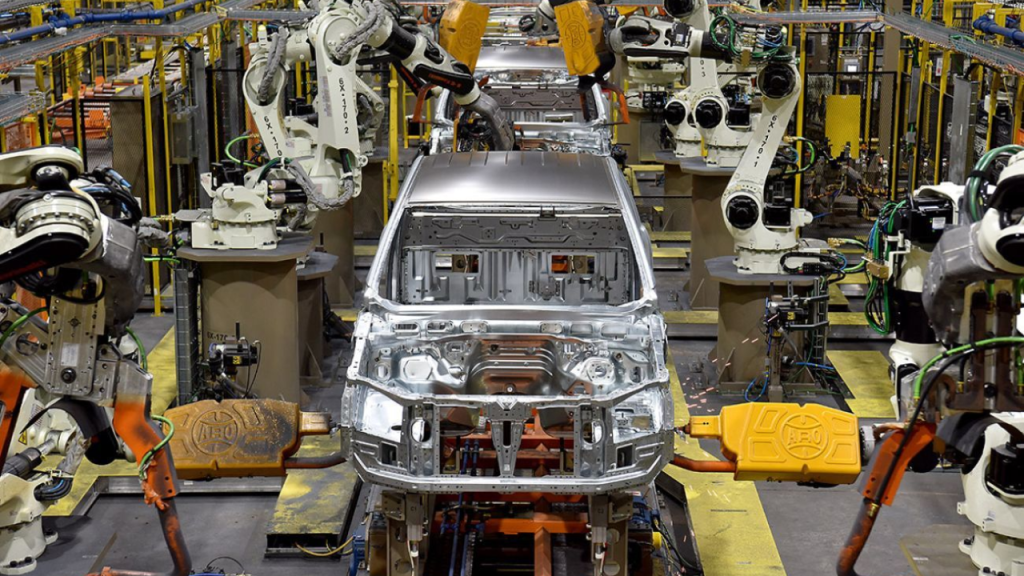
While the construction of entirely new assembly plants takes years, there are ways to increase U.S. production more quickly. Automakers can ramp up production at existing plants that already have established supply chains and workforce infrastructure.
This approach is far less costly and much faster.
For example, General Motors (GM) increased production of its Chevrolet Silverado pickup trucks by expanding production at its plant in Fort Wayne, Indiana, soon after the 25% tariff was imposed.
This move allowed GM to meet demand without the need for a new plant or extensive capital investment. However, such quick fixes are limited and often apply to high-volume vehicles that can be easily scaled.
Plant Conversions: A Costly but Effective Solution
Another approach is to convert existing plants to accommodate new models or to increase capacity. Jeep’s parent company, Stellantis, spent $1.6 billion converting two powertrain plants into a new assembly plant in Detroit, marking the first new assembly facility in the area in nearly 30 years.
This project took around two and a half years to complete and serves as an example of how conversion projects can bring new production lines to the U.S. at a relatively fast pace.
But even these conversions are not without challenges. In 2019, Ford spent $1 billion to retool its Illinois plant for the Ford Explorer SUV. Despite the quick turnaround, the project faced numerous difficulties, costing Ford billions in recalls due to flawed production processes. These situations highlight the risks involved in attempting to increase production too quickly.
Moving Forward: A Pragmatic Approach
Industry leaders, such as Swamy Kotagiri, CEO of Magna, a major auto supplier, stress the importance of taking a pragmatic approach. “It’s not as easy as just picking up and moving,” Kotagiri said.
The challenges in production relocation are not only about time and money but also about maintaining a stable regulatory environment. Constant changes in trade policies or regulations can add uncertainty, making it difficult for automakers to commit to large-scale production shifts.
Despite these challenges, automakers are making efforts to adjust their production strategies to meet new demands. Whether by using existing capacity, converting plants, or investing in new facilities, manufacturers are working to align with Trump’s policy while keeping their operations viable.
Conclusion: The Road Ahead
Increased U.S. vehicle production, as envisioned by Trump, is not impossible, but it will take time and considerable investment. While some companies are already increasing output at existing plants, building entirely new facilities will require years of planning and construction.
As the automotive industry moves forward, a balanced, pragmatic approach will be key to overcoming the complex challenges posed by relocating production lines to the U.S.